ISO 9001 Certification Audits
In today's competitive business landscape, maintaining high-quality standards is paramount for organizations striving to meet customer expectations and drive continuous improvement. ISO 9001, the internationally recognized standard for quality management systems, provides a framework that enables organizations to establish robust processes, enhance customer satisfaction, and achieve operational excellence.
What is ISO 9001
ISO 9001 is an international standard for quality management systems. It emphasizes a process-oriented approach, customer focus, continual improvement, involvement of people, evidence-based decision making, and risk-based thinking. Organizations that achieve ISO 9001 certification have implemented a systematic approach to consistently meeting customer requirements, enhancing customer satisfaction, and driving ongoing improvement.
Key Benefits of ISO 9001
- It leads to improved customer satisfaction by focusing on meeting customer requirements and promptly addressing concerns.
- ISO 9001 promotes organizational efficiency through streamlined processes,
- reduced errors, and better resource utilization.
- Certification enhances credibility, reputation, and opens doors to new business opportunities.
- It strengthens internal management, fosters better supplier relationships, and ensures regulatory compliance.
- Ultimately, ISO 9001 drives positive change, customer satisfaction, efficiency, and long-term organizational success.
What further Benefits can I expect
- It helps establish a culture of continuous improvement,
- This leads to increased employee engagement, motivation, and professional development
- Reduced operating costs
- Improved stakeholder relationships
- Improved risk management
- Proven business credentials
- Openings in new markets
- Customer satisfaction
How is ISO 9001 Structured
ISO 9001 follows a structured framework that consists of several key components:
- Scope: The scope defines the boundaries of the quality management system (QMS). It specifies the products, services, processes, and locations that are covered by the QMS.
- Normative references: ISO 9001 references other relevant standards and documents that are applicable to the QMS, ensuring alignment with best practices.
- Terms and definitions: This section provides a list of key terms and definitions used throughout the standard to ensure consistent understanding and interpretation.
- Context of the organization: Organizations are required to determine the internal and external factors that can impact their QMS. This includes understanding the needs and expectations of interested parties, such as customers, employees, suppliers, and regulators.
- Leadership: This section emphasizes the importance of leadership and top management commitment to the QMS. It outlines the responsibilities of management in establishing and maintaining the QMS, as well as promoting a quality culture within the organization.
- Planning: Organizations are required to plan and establish quality objectives that are aligned with their overall business goals. This involves identifying risks and opportunities, determining actions to address them, and allocating necessary resources.
- Support: This section addresses the resources, competence, awareness, and communication requirements for effective implementation of the QMS. It emphasizes the importance of providing adequate training, infrastructure, and support to employees.
- Operation: This part focuses on the execution of the QMS processes, including planning and controlling operational activities, product/service design and development, and controlling external providers (suppliers).
- Performance evaluation: Organizations are required to monitor, measure, analyse, and evaluate the performance of their QMS. This includes conducting internal audits, collecting, and analysing data, and assessing customer satisfaction.
- Improvement: This final section emphasizes the importance of continual improvement. It outlines the requirements for taking corrective actions, addressing nonconformities, and implementing preventive measures to enhance the effectiveness of the QMS.
The structure of ISO 9001 follows a plan-do-check-act (PDCA) cycle, which reflects the iterative nature of quality management. This cycle is integrated into the various sections of the standard, encouraging organizations to continually plan, implement, evaluate, and improve their QMS.
Who can apply for ISO 9001 certification
Any organization, regardless of its size, type, or industry, can apply for ISO 9001 certification. ISO 9001 is applicable to both product and service-oriented organizations, including manufacturing, healthcare, construction, IT, education, and many others. It is not limited to specific sectors or regions. Whether a small business, a multinational corporation, a non-profit organization, or a government entity, any organization that aims to enhance its quality management systems and demonstrate a commitment to meeting customer requirements can pursue ISO 9001 certification. The standard provides a flexible framework that can be tailored to suit the unique needs and context of each organization, making it accessible to a wide range of entities seeking to improve their quality practices and gain a competitive edge.
Requirements for the ISO 9001 Standard
The ISO 9001 standard sets out specific requirements that organizations must fulfil to achieve certification. These requirements include:
- Context of the organization: Understand internal and external factors, identify interested parties and their needs.
- Leadership: Demonstrate commitment, establish quality policies, and foster a culture of quality.
- Planning: Address risks and opportunities, set quality objectives, and develop plans.
- Support: Provide resources, infrastructure, and competent personnel. Ensure effective communication and awareness.
- Operation: Control processes, manage requirements, handle design and development, purchasing, and production/service delivery.
- Performance evaluation: Monitor, measure, and analyse performance through audits, customer satisfaction evaluation, and data analysis.
- Improvement: Take corrective and preventive actions, seek continual improvement opportunities.
- Documentation: Maintain records, document procedures.
- External audits: Undergo audits by accredited certification bodies.
What is the Certification process
The certification process is in three simple steps:
- Application for certification
- Complete the online enquiry form and we will get back to you with quotation.
- Initial Certification Audit
The assessment process is based on a 2-stage approach as follows:
Stage 1 – A basis audit to check whether the organisation is in a state of readiness for the stage 2 audit and involves the following:
- Confirm that the quality system conforms to the requirements of the ISO 9001
- Confirm the scope of certification.
- Production of a report that identifies any non-compliance or potential for non-compliance and
- Agree a corrective action plan if required.
- Production of an assessment plan and confirm a date for the stage 2 assessment visit.
Stage 2 – the purpose of this visit is to confirm that the quality management system fully conforms to the requirements of ISO 9001 in practice and involves the following:
- Undertake sample audits of the processes and activities defined in the scope of assessment.
- Document how the system complies with the standard.
- Report any non-compliances or observations.
- Produce an audit programme and confirm a month and year for the first surveillance visit.
IAF Cert Search
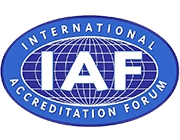
The IAF Cert search is a global database where users can search and validate the status of accredited certifications issued by a Certification Body which has been accredited by an IAF MLA Signatory Accreditation Body
This means that anyone can validate an organizations certification(s) confidently knowing, the certification is valid, the Certification Body is accredited, and the Accreditation Body is a current IAF MLA Signatory member, in real time, all in one process.
Download an introductory presentation to find out more.
Validate a Certificate here.
UKAS CertCheck

The UKAS CertCheck is a global database where users can search and validate the status of accredited certifications issued by a Certification Body which has been accredited by UKAS.
This means that anyone can validate an organizations certification(s) confidently knowing, the certification is valid, the Certification Body is UKAS accredited, in real time, all in one process.
Validate a Certificate here.
For more information about our services please contact us by using our contact form, by phone or drop us an email. We will be pleased to assist you.
Alternatively get a quote by filling in our enquiry form